We aim to reduce waste from production and increase efficiency in the use of raw materials. Our ambition to decouple growth from increasing material use goes beyond recycling. It starts with limiting the need to recycle. Therefore, we focus on zero waste, working to the ‘right first time’ principle and repurposing and reclaiming materials. We are on a journey to become a zero-waste company in both material waste and water. This includes ambitious targets of zero waste to landfill and reusing water at the most water intensive sites by 2030, as well as implementing closed water loop systems in all production environments.
We believe that local partnerships with customers, suppliers, and other industry sectors are what will pave the way to decouple growth from limited resources. That’s why we were honoured to be invited to participate in Dassault Systèmes’ series ‘Future Models’ showcasing companies in Sweden that innovate for sustainability. Watch the video to understand how our R&D teams work to revolutionise care for people and planet.
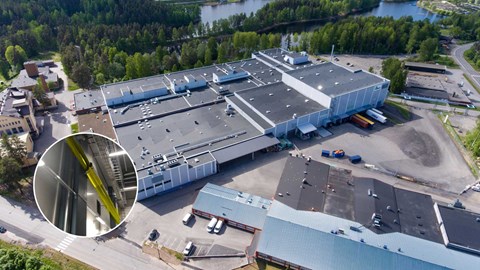
We are committed to continuously reduce the use of energy resources delivering environmental benefits and generating cost improvements. In 2022 we implemented a heat recovery system in our Mikkeli plant to build a closed energy loop, contributing to our commitment of net zero GHG emissions by 2050 the latest. The heat is collected from various processes such as the coating line, the foam line and the trim waste exhaust. By replacing the use of external fuel for heating or cooling of all production and office areas, the new heat recovery system will cut externally purchased heat by 70% in the Finnish factory and help reduce Scope 1 emissions by 350t CO2eq. annually.

Taking action on minimising waste
During 2022, thanks to a partnership with a local waste recycling company, Mölnlycke’s two Czech factories moved away from landfilled waste to reusing or recycling the different streams after proper segregation.
Cardboard and paper are now recycled into new fibres in local paper mills, plastic waste and foils are processed into re-granulates, which are then used to produce new foils for plastic bags. Wood packaging is crushed into wood chips and turned into certified fuel for energy use in sugar factories. These activities resulted in more than 95% of all the waste produced at both sites being reused or recycled in 2022.
Similarly, our surgical glove manufacturing plants in Malaysia recover raw materials, such as natural and synthetic latex, and collect them at the end of production for reuse in new production processes in line with the circular economy principles, contributing to a 97% waste diverted from landfill across all glove sites.
By providing local businesses with access to high quality and convenient materials as an alternative to virgin raw materials, together wiht our partners we are promoting a circular economy based on reuse and recycling.
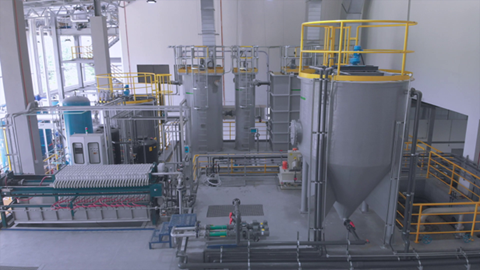
We look beyond traditional water efficiency and regulatory compliance. We are continually assessing water risks and social impacts related to water sources and security of supply at selected sites. We strive to reduce the impacts to a minimum, by:
- implementing good maintenance practices of machineries and secondary containment measures at all factories,
- containing spills of raw materials through preventive maintenance,
- good operation procedures,
- training employees and suppliers involved in raw material
management.
For each production site located in areas of concern, we develop water action plans, tailored to the local context, including how to improve water conservation and water reuse. For example, Business Area Gloves has set the ambition of achieving a closed-loop process for water systems at all its sites and to continuously decrease water consumption. A state-of-the-art solution for water treatment has been installed at our newly opened surgical glove factory in Kulim Hi-Tech Park anticipated to reduce water consumption, as well as improve the plant's wastewater management and the disccharge quality.
Finally, all operation teams consistently share best practices for optimised water use during routine and non-routine tasks and educate and engage employees on water conservation.

Packaging
Packaging has an important role to play by extending the lifespan of Mölnlycke’s solutions and protecting them from external factors such as damage during transport and handling, or deterioration caused by contamination. This reduces the need for additional raw materials and resources in products and helps to minimise waste for customers.
However, packaging also presents some challenges. It uses valuable resources in manufacturing and generates waste when not recycled – an increasing focus of governments and regulators around the world.
As part of our resource efficiency journey, we have set a target that more than 95% of packaging will be recyclable and more than 80% of all packaging made of post-consumer recycled (PCR) and/or renewable material by 2030. These targets are based on total packaging weights and 2022 product scope1. Currently, 91% of the packaging material was recyclable and 72% contained recycled material.
The majority of the our primary packaging is made of mixed plastic or composite materials. This presents recyclability challenges considering currently available end-of-life infrastructures. We are developing solutions to these issues. In the Antiseptics product assortment, all bottles and ampules are made of 100% recyclable mono-material plastic. We will continue to work with suppliers, recyclers and other partners to increase recyclability for plastic primary packaging in other business areas, as well as optimising their weight and recycled content.
1 Scope covering products mainly produced by Mölnlycke, most contract manufactured and distributed products excluded from the initial scope. Scope to be increased during 2023.